Plastics Makers Plot the Future of the Car
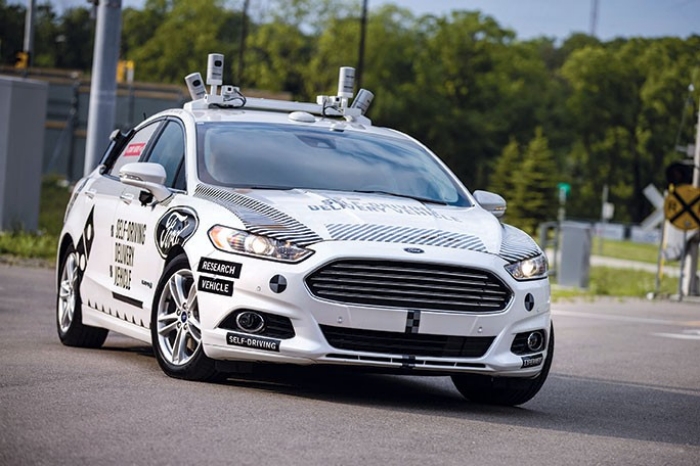

(Adapted from article written by Alexander H. Tullo and published on C&EN)
While companies work on autonomous vehicles, the global stock of cars is slowly electrifying. Some 750,000 plug-in hybrid and fully electric vehicles were sold worldwide last year, representing about 1% of the total car market, according to the International Energy Agency (IEA). U.S. consumers bought 160,000 hybrid and electric vehicles last year. About 2 million hybrid and electric vehicles are on the road today, IEA reports. By 2020, that number will climb to between 9 million and 20 million, the agency expects, and from there it will more than triple by 2025.
Demand will increase for plastics used to make connectors and housings for the many electrical and electronic components required for both electric and autonomous vehicles. The use of plastics for parts unique to internal combustion engines, such as fuel lines and air intake manifolds, will gradually decline. Plastics makers see opportunity in the auto industry’s evolution. The changes will place a premium on high-end materials that can withstand the extreme heat and electrical conditions in electric and autonomous vehicles.
Polymers reduce vehicle weight when they replace heavier materials such as metal and glass, saving energy. For every 10% of vehicle weight reduction, fuel economy improves by about 5%. The amount of plastics used in automobiles has increased over time. In 1960, the average car made in North America had only 8 kg of plastic and composite materials. In 2016, the typical car was made with 151 kg of plastics and composites. This represents about 8% of the car’s weight and about 50% of the volume of materials in the car.
Companies are also developing new materials. DSM has introduced ForTii Ace, a modified polyphthalamide with a glass transition temperature of 160 °C, about 40 degrees higher than other polyphthalamides and 80 degrees higher than nylon 66, a common polymer used in applications that confront heat. The material can withstand these temperatures without organic heat stabilizers, the addition of which could lead to corrosion of electronics. A typical application might be in connectors for a circuit board that houses important central processing unit chips and is connected to sensors from around the vehicle. Some things polymer makers do know for sure. Applications such as oil pans and fuel tanks will disappear in time. But polymers will pick up gains in other areas. Their role will evolve, but they will be as crucial to cars as they are today.

Subscribe
