World-class Highly Anti-corrosive Surface Treatment Expert from Japan -- Nihon Ruspert Co. Ltd.
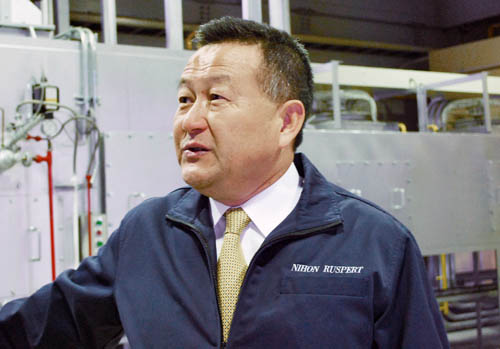
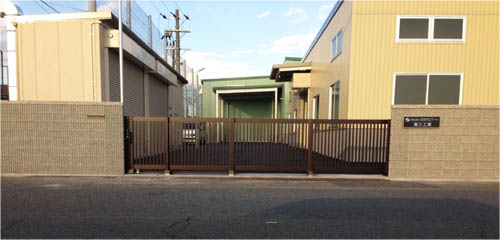

Established in 1968, Nihon Ruspert specializes in anti-rust surface treatment for steel parts. Its main business includes surface treatment service, specialized chemical agent manufacture, giving processing authorization to other surface treatment companies, and selling chemical agents. The main equipment it sells is dip-spin coater. Through its well-acclaimed thin-coat and highly anti-corrosive metal surface treating technology, it processes fasteners for construction, machinery, power generation among other industries. Recently its orders in the new energy (solar/wind) sector are increasing. Its advantage is one-stop surface treatment, ranging from steel surface adjustment to electroplating and even lubrication, for all sorts of metal. It offers various products including galvanization, steel/stainless steel sand blast, anti-rust fastening torque adjustment, and anti-galvanic-corrosion treatment. It has a base in Kyodai Katsura Venture Plasa. CEO Masayuki Tsumura explained, “The future development of surface treatment and environment technology cannot lack a high degree of industry-academia collaboration. Utilizing the Plasa, we can witness unfathomable new inspiration from other companies and collaborate with them, cultivating high-value talents and technology.”
5 Coating Series on Your Demand
Back in the 80’s, composite treatment combining galvanization and coating was favored by European customers suffering from acid rain. Nihon Ruspert’s world-class highly anti-corrosive surface treatment is well acclaimed by the construction industry. Particularly Ruspert Series is characterized by the abundance of type tailored to market demand, including the R&D and rollout of Non-chrome Ruspert. For non-galvanization applications, the company developed Disgo Series in the 90’s and entered the zinc flaking territory, even adding the hot-galvanizing type that became the main product along with Ruspert Series, both applied in civil engineering, electric power, conveyor, etc. Extending zinc flaking technology, Lafre Series suits automotive fasteners stringent with coating thickness. Other series are Nicoa with high corrosive gas resistance and Drall that dries and repairs surface under room temperature.
Rooting Across U.S./Europe/Aisa & Eyeing the World Market
The CEO said wherever a product needs his surface treatment, that region is his target market. “In southeast Asia with increasing fastener production, selling chemical agents is one of our business pillars. In Europe, there’s no sign of consumption increase but there are many international corporations based there; therefore the geographic advantage is the ability to get closer to orders, designs and new technologies from the world. Establishing bases in rapidly-growing southeast Asia and immense/mature Europe is very favorable to us.” Taiwan and China are important regions as well because most fastener production that adopts surface treatment gathers there. This region has a higher number of authorization and chemical agent sales proportion, and the products are mostly sold to N. America, Europe and Japan. “The emerging ASEAN and surging personnel expenses decrease price competitiveness and lower the position of Taiwan and China, but they will remain primary regions of fastener production in the next few years,” said the CEO.
To the Era of Environmentally-friendly Coating
“Due to market demand and global pollution problems, the world is more stringent about hazardous substance. The regions that cannot easily conduct electroplating due to water discharge regulation will have particularly high demand for zinc flaking, and will switch from solvent to water-based coating. Environmentally-friendly coating in response to the demand of this era is expected to embrace a high demand and won’t be subject to the changing world demand and supply balance caused by politics and exchange rate.” The company will exhibit Caelar (effluent-free electroplating) and water-based coatings at IE expo this May. “We will make a better, healthier and more natural world a reality by technical innovation of metal surface treatment. Look forward to our new technology for a safe and bright future.”

Subscribe
