Innovative Feeder: Ming Tang Machinery Releases New Centrifugal Feeder
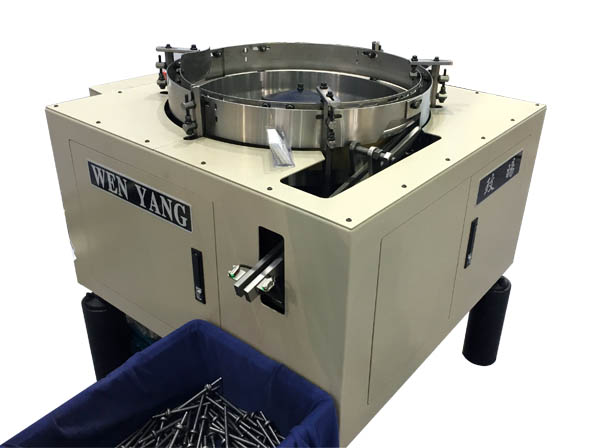
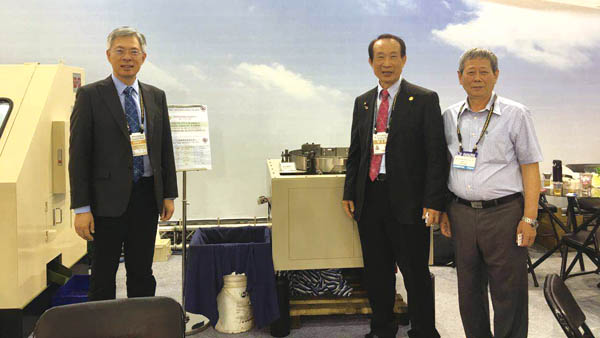

Ming Tang Machinery Co., Ltd has years of experience in manufacture for open die headers and screw/washer assembly machines. Its products include 1-die 2-blow screw headers, 2-die 4-blow screw/part formers, and 3-die 6-blow screw/part formers. It also develops and produces new screw/washer assembly machines. It has a complete range of machines with excellent quality. In addition to CE approval, it has acquired many new patents and is recognized by the industry.
Why and How This Centrifugal Feeder
was Created
Conventional feeding systems always adopt vibrating plates for material feeding, which causes noise during the feeding process and troubles the clients and in-house operators. In order to deal with this problem, Ming Tang started to develop the centrifugal feeder. After 2 years of R&D and several times of discussion, design, planning, and trial run repeatedly, the new machine, which can align materials in a centrifugal way and smoothly achieve significant noise reduction, was eventually created.
This new feeder has more advantageous features. When clients’ products are coated or electroplated, these products inspected by sorting machines with conventional vibrating plates often show peeled coatings and damaged electroplating layers, whereas the new centrifugal feeder using the centrifugal force to align materials can replace conventional feeders with vibrating plates, greatly reducing the possibility of product damage. The body of the centrifugal machine is made of stainless steel, which is wear and corrosion resistant. Conventional vibrating plates have excessively thin coatings and the coatings will usually peel off after around a year of operation, whereas the internal plate of the new centrifugal feeder has a 10mm-thick PU oil-based coating that is expected to resist wear and oil. Besides the two advantages mentioned above, Ming Tang added that the new feeder is also installed with a specially designed removable internal plate to better cope with oil drop or iron scrapes frequently observed in machine operation and reduce procedures for onsite maintenance. Such a thoughtful design for clients is really admirable.
Popular Critical Functions
Ming Tang’s centrifugal feeder shows the following features: (1) Reduced noise; (2) Applicability to long screws; (3) Preventing collision and reducing damage on extenal appearance; (4) Reducing surface damage of coated or electroplated products; (5) 1/10 of power consumption of the common vibrating plate; (6) Removable central circular plate for cleaning iron scraps and oil stains; (7) Adjustable speed by an inverter; (8) The internal plate has a 10mm-thick PU oil-based coating that is oil resistant, more durable, and non-peeling as compared with the surface coating of average vibrating plate. After the debut of the centrifugal feeder type 720 at Taiwan International Fastener Show this April, it has caught the eyes of many domestic and overseas clients placing their orders for this model.
Vice general manager Sam Chang says, “In the future we will roll out centrifugal feeders (type 1000 and type 1200) that are bigger and designed for feeding longer screws ranging from 200mm to 500mm.” Let us look forward to the next innovation of Wen Yang.

Subscribe
