News
Reflecting on Taiwan Hand Tool Industry Through the U.S. Hand Tool Supply Chain Crisis
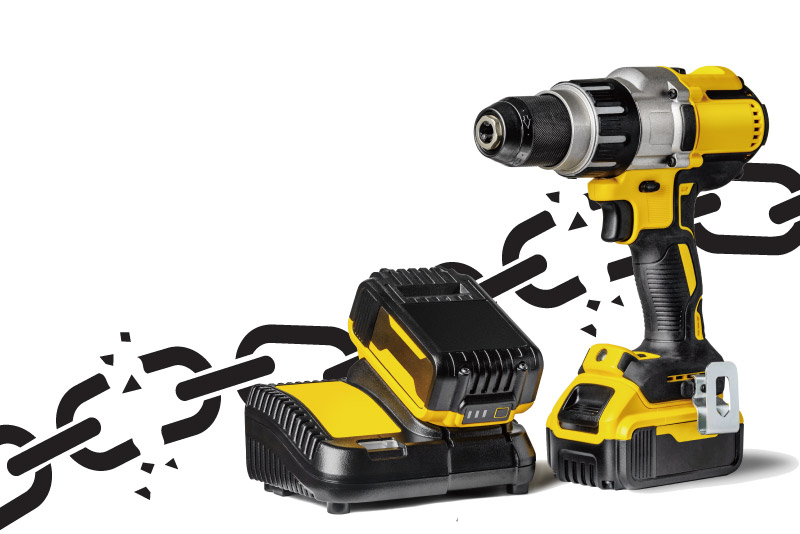

Add to my favorite
2024-05-24
Exiting Hand Tool Manufacturing?
The Missing Puzzle in U.S. Hand Tool Manufacturing
Last March, Stanley Black & Decker announced it was closing the highly automated hand tool manufacturing plant in Fort Worth, Texas, which had been established for 3 and a half years and cost 90 million U.S. dollars, mainly producing the "Craftsman" tools which is a brand acquired by Stanley. This move is to save US$2 billion in costs. Before long, this March, Stanley announced the closure of the US$31 million manufacturing plant in Fort Mill, South Carolina (which produces "DeWalt" brand tools), also for cutting costs. Words emerged that Stanley was looking to reduce its bases in Asia. The Wall Street Journal devoted an article to explore why the leading American hand tool company cannot produce hand tools in the United States. It said the company just can't figure out how to make wrenches, and criticized that the Fort Worth factory sought to use unprecedented high automation and efficient production to bring the luster of "Made in America" back to the United States, but that in the end it proved to be a huge failure due to slow production speed and equipment problems.
In fact, Stanley was not the one that fired the first shot. In 2020, Ideal Industries announced the closure of its Western Forge brand (once the largest screwdriver manufacturer in the United States) and its U.S. factory. In 2017, Apex Tool Group announced the closure of the Armstrong brand and South Carolina factory.
Talent Gap
Back to the Stanley case. Internal sources pointed out that the Fort Worth factory was originally going to produce high-quality hand tool products that could compete with "Chinese prices" through the development of unique automation technologies new to the industry. These technologies aimed to convert manual manufacturing processes into automated production and at the same time significantly improve product yields, but something went wrong in the process. Wrenches and ratchets become misshapen after passing through the press, resulting in millions of dollars spent on equipment adjustments. There is also the issue of sockets not being fully punched. In other words, the yield target couldn’t be reached. Another problem was losing experienced senior craftsmen with in-depth knowledge of tool making at the time, which added to the predicament. This reveals the problem of technical talent gap at the Fort Worth plant.
Automation technology can solve many problems in this challenging era, but successful technology research and development must be supported by talents with professional manufacturing knowledge. In the manufacturing of hand tools such as wrenches, even with automated machines, "human-owned craftsmanship" is still critical. Developing and tuning automated machines may sound simple to laymen, but in fact, whether it is forging or heat treating, the professional knowledge and flexible thinking of human brains are often something that automated machines cannot easily simulate or match. It is quick and simple to think with a human brain, but it will be very complicated to convert into a computer program. Therefore, experienced talents are indispensable.
Lack of a Full Supply Chain
Beyond that, there are structural issues. A long time ago, "Made in the U.S." once dominated the manufacturing market, but now manufacturing in places outside the United States has become the norm. For years, U.S. manufacturing has spread production overseas to reduce costs, which comes at the cost of sacrificing an intact domestic supply chain. Just like the fastener industry chain, hand tools also require a specialized industry chain. The key competitiveness brought by a domestic industrial chain is the rapid acquisition and exchange of technical knowledge, raw materials and tools domestically, the improvement of overall price competitiveness through a mechanism of coexistence and mutual benefits, and the ability to provide complete supporting services. This is the key piece of the puzzle that the U.S. hand tool industry does not possess. Even if U.S. manufacturing has returned in recent years, rebuilding the U.S. hand tool supply chain is not something that can be accomplished in the short term.
Low Price Competition
In addition, more and more people just want to buy hand tools with lower cost, and there are many imported low-price hand tools in the U.S. market. Amid low-price competition from overseas peers, it is a big challenge for American hand tool companies to find a balance between high labor costs and price reduction.
The U.S. Leaves a Vacant Spot for Taiwan and China to Fill In
Taiwan's hand tool manufacturers are in sharp contrast to the Fort Worth factory. There are approximately 2,400 hand tool manufacturers in Taiwan with nearly 50,000 employees. Seventy percent of these manufacturers gather in central Taiwan to form a very special industrial cluster in the world which comes with a complete supply chain, covering dies making, heat treatment, forging, electroplating, assembly, as so on from processing to finished products. This cluster creates an output value exceeding NT$130 billion a year. More than half of the hand tool products supplied by international brands are actually made in Taiwan. For example, Yih Cheng Factory based in Taiwan is the leading OEM manufacturer of American screwdrivers, with an annual output of more than 35 million screwdrivers.
Although Taiwan faces shortages in water, electricity, workforce, land, and funds, its hand tool industry still possesses sufficient "craftsmanship". Even if it does not have the most advanced automated production technology comparable to European and American counterparts, it can respond to various demand from global customers in real time. Coupled with the support of a complete supply chain, finished products in full sets can be provided to overseas buyers. Craftsmanship and supply chain are the keys to the success of Taiwanese hand tools. On another note, the Hannover Messe this year can also give us some inspiration. This exhibition showcased the latest technologies in the fields of automated robotic arms, smart manufacturing, and Industry 4.0. Upon the requirements of unmanned, automated and systematized manufacturing, the manufacturing industry is facing cost pressures for upgrade and transformation. However, the industry can’t afford to stop the pace of transformation, so companies must modify their practices as they go. Strategic alliances for new energy technologies have emerged in Europe, and coupled with the ESG and CBAM trends that have followed, the development of new energy policies will change the design and manufacturing of tools in the future. Should it be regarded as a crisis or a turning point? That is for you to make a judgement upon.
To that, the big players of Taiwan hand tool industry have been upgrading themselves to create high-value products for high-end industries. For example, Proxene Tools continues to delve into technology and has launched adjustable wrenches for the U.S. defense and aerospace industries. In addition, it introduced robotic arms into its factory, redesigned its workstation flow, introduced automated warehousing, and successfully set up a smart production line that increases production capacity by 30%. Today, Proxene Tools is one of the top three industrial adjustable wrench manufacturers in the world, accounting for a quarter of the market.
In recent years, there has been little growth in the production capacity of hand tools in Europe and Japan, and some of the major American factories have closed down, so some orders have been redirected to Proxene Tools. Even so, that doesn’t mean Taiwan hand tool manufacturers have no tough competitors. China's “red supply chain” has caused intense low-price competition with Taiwan. The price of Chinese DIY hand tools is only half the price in Taiwan. Therefore, the big players of Taiwan hand tool industry are transitioning to high-end professional-grade tools and carbon reduction.
Not only that, Taiwan is using its supply chain advantages to build an all-star alliance of hand tools. Machan International will be the leader in forming a strategic alliance with six well-known Taiwanese hand tool manufacturers, including K&W Tools, Kuang Yuang Industrial, Gong Maw Enterprise, Proxene Tools, Lucky-Brand Industrial and Yih Cheng Factory. They will be collaborating to provide solutions to global buyers. On another note, these companies are advised to learn from the successful experience of Taiwan fastener industry. The fastener industry in Taiwan has begun to shift from pure manufacturing to marketing, and the overall scale of this industry is larger than that of the hand tool industry. Among all fastener manufacturers in Taiwan, more than 35 companies account for 50% of Taiwan's total fastener export value, including many large companies with a turnover above 100 million US dollars. Only when a company is large in scale can it have enough capital to step out of the box of pure manufacturing and go ahead with mergers and acquisitions, as well as create brands or establish marketing and warehousing bases overseas. If Taiwan hand tool industry can cultivate large-scale enterprises of international scale, they can drive the positive development of small and medium enterprises in the entire hand tool supply chain.
Taiwan and China are actively filling the gap left by American hand tool manufacturing. The lesson to take away from this story is to cultivate a specialized supply chain. Secretary of U.S. Commerce Gina Raimondo was interviewed in the CBS News program "60 Minutes", where she told the host: "We have the most sophisticated semiconductors in the world." The host asked her if 'we' include Taiwan. She replied it's "fair" to include Taiwan in her use of “we.” The same revelation has occurred in the U.S. semiconductor industry, which many readers have already witnessed. The importance for the hand tool industry to maintain its own intact supply chain is self-evident.
扣件
國際展會
惠達雜誌
匯達實業
外銷媒合
廣告刊登
螺絲五金
五金工具
紧固件
台灣扣件展
印度新德里螺絲展
越南河內螺絲展
墨西哥瓜達拉哈拉螺絲展
美國拉斯維加斯螺絲暨機械設備展
波蘭克拉科夫螺絲展
義大利米蘭螺絲展
德國司徒加特螺絲展
FAIR INDIA
FASTENER FAIR VIETNAM
FASTENER FAIR MEXICO
FASTENER POLAND
FASTENER FAIR ITALY
FASTENER FAIR GLOBAL
FASTENER WORLD