Industry Activities
Sacma Group- Cold and Warm Forming Machines Capabilities
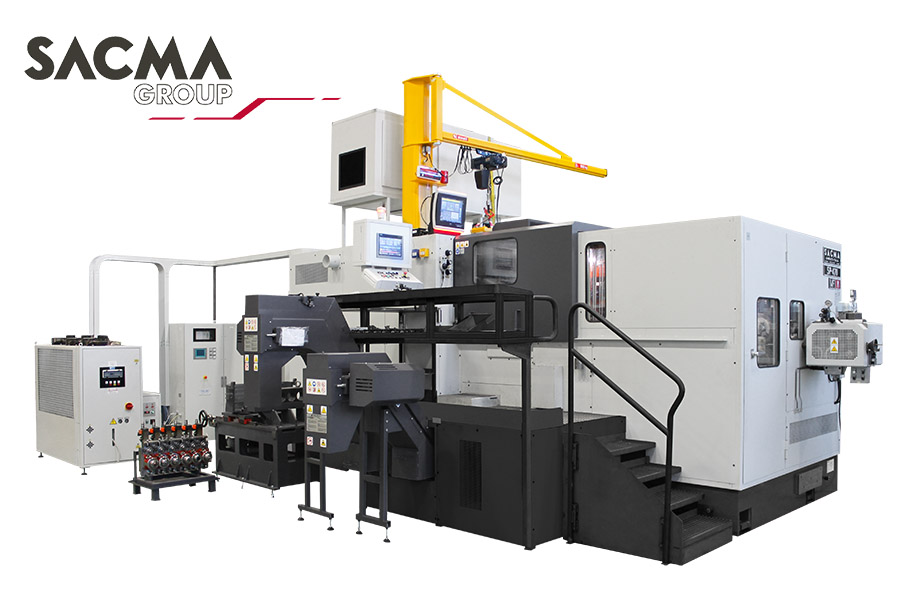

Add to my favorite
2024-05-23
Today the variety and the quantity of metal fasteners produced by cold forming of wire rod is impressive. Almost all of screws, bolts and nuts are made with that technology, but not only. The name of the process evokes itself the capacity to form a lot of special parts, solid or hollow, with a complex shape, to be used in the most important industry fields, automotive first. The cold forming is not anymore the simple heading of its debuts in the early fifties. By sophisticated multiple die presses, dedicated materials, accurate tooling, it becomes possible to produce parts that only few decades ago no one could imagine obtaining from wire. If we add the advantages coming from a high productivity, optimal use of raw material, consistency of precision, the success and the spread of this technology appears logical and motivated. There is another important point in favour, especially these days. I mean about his intrinsic sustainability, derived from the modest energy intake and the minimal scrap rate.
In Sacma, we are always working to build, in a sustainable way, sustainable machines for the most sustainable technology. To do that, we chose solutions requiring low energy consumption, we increase own production of renewable energy, and we select accordingly our supply chain. The core activity of SACMA Group is to design and build machinery for cold forming process, a complete line of presses and rollers to fulfil the needs of the modern industry, including ancillary equipment and machines for secondary operations. Our mission is to offer to the producers of cold formed parts the best possible equipment with effective solutions, keeping at the same time the well-known robustness and reliability of Sacma machines.
Looking to the most innovative solutions recently introduced, I would like to start with the mechatronics application. In our machines there are more and more functions activated by servomotors: wire feeder, stock gage, die kick out, transfer, starter… The purpose is to make easier, intuitive and quicker set-up of the machine, with more safety for the operator, because reducing their manual interventions, allowing to activate and control the operations directly by HMI. We started to introduce those functions in the bigger sizes of presses, where the advantage for the operators is more consistent, and gradually we are implementing also in the small machines. Ever focusing the user’s needs and the work environment, we re-designed the machine cabins, integrating inside them all the items, like the main motor and the lubrication unit, which were previously external. The result of this activity is a more compact machine, less floor consuming and emitting a lower noise level. Also, any oil dropping is eliminated, to keep clean and healthy the work room. We also improved the ergonomics with more comfortable doors and internal spaces for the interventions. The action plan is already in progress, with the target to fit all the machine models within the next year. Coming now to functions more connected with the cold forming, Sacma continues to develop and to propose solutions which scope is to enlarge the potential of this technology.
It’s known that complicate parts made with alloyed steels cannot be formed in one shot, even through more forming stations. The material, stressed by a too high deformation rate, starts to crack. To avoid that, must proceed with an intermediate heat treatment to regenerate the metallographic structure. The production process becomes articulated and involving more machines. Sacma introduces the re-feeding equipment, allowing to apply the two steps process in the same machine, at the same time. Another solution for extended deformation sequences is the device for feeding pre-formed parts in the cut off station. By that, having a 6 die press, it should be possible to execute a deformation in 12 steps, with an annealing/coating operation in between. All done starting from a standard machine.
In optics to extend the borders of cold forming, SACMA is constantly involved to improve own WF machines. The warm forming technology is very near to the cold forming: same base machines, same concept of tools, only a special equipment, making them suitable to work at the temperature enlarging the deformability of difficult materials, like stainless steels, titanium alloys and nickel superalloys. Sacma recently presented a complete line of WF part formers, split in different model according to the operating temperature: WF300, WF500 and WF900, to work respectively up to 300°C, up to 500°C and up to 900°C, based on the parts and the materials to be produced. The program predicts all the machine sizes and, thanks to the Sacma Modular Design Concept all the machine models could be involved. Also, Ingramatic offers a complete line of WF rollers, for threading aerospace fasteners.
An interesting function could be integrated in all our machines is the thermoregulation of the die box and the cooling oil tank. When the tolerances of the part become tight, a stable temperature of tools and coolant is the priority. The TR unit is positioned nearby the machine, to heat up the die box and the oil at machine start. Afterwards, during the production, it cools down, keeping them inside the desired range of temperature. Thermoregulation means precision and consistent reduction of NC parts. That function can be implemented in the WF machines, and it is effective for the cold formers, too.
The combined machines are for SACMA a key product, since the first one, an SP27 still active at our Italian customer, left the Limbiate factory in 1974, something like 50 years ago. All in one production centre, including forming, pointing and thread rolling. One single machine, compact layout, quick plug in, sealed. One main motor moving all the units, high efficiency and energy recovering. The most effective and sustainable solution to produce threaded fasteners and not only. Those machines, suitable for products in the range from M3 to M24, are constantly innovated and improved by our engineers, focusing the easy use, the quick tool change and the energy consumption. Already in catalogue we have the SP59, in two versions, normal and short stroke. She’s a 6 die combined press, extending the range of products to the more complicated special parts. In the next period we will present the SP39 and following also the SP29. Considering that the WF equipment should be available, the flexibility in terms of feasible products becomes without comparison. Always on the subject of combined machines, Sacma is proposing the new KSP12, a fully re-designed successor of the iconic KSP11, an 1D2B header with thread rolling, suitable for production of screws, self-tapping and metric, from diameter 3 to 8mm. The machine was enthusiastically accepted by our loyal customers and by new, too. The world preview occurred during the last Wire Düesseldorf, and the next step is to present a new version for ultra short and small head screws.
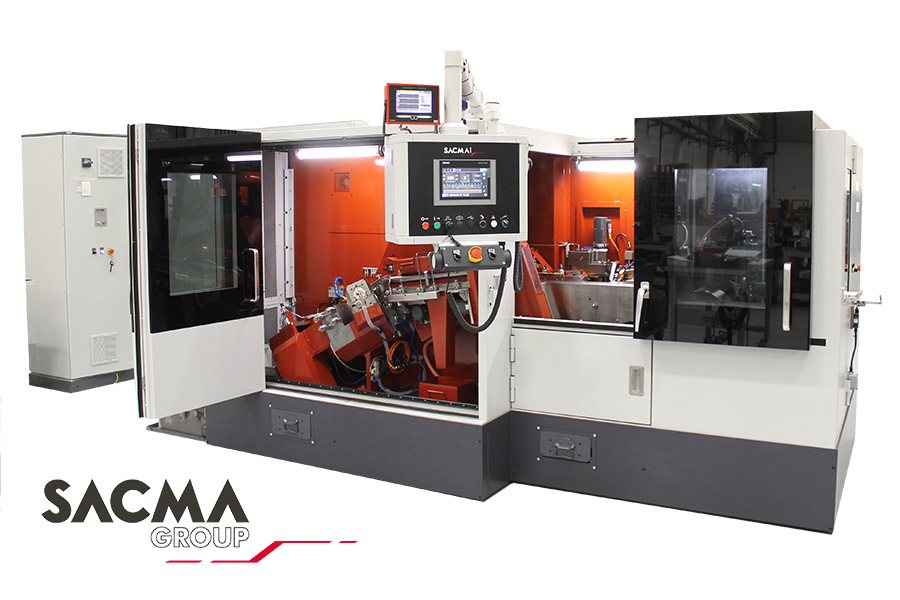
(KSP12 Machine)
Being aware that the best machine to squeeze high performance needs the best tools, Sacma introduced recently for own customers the S-Tooling activity. In a structural way, we created a department, where skilled and experienced engineers develop and design the tools for new complex parts inquired by the market. They are supported by the most up to date and innovative instruments for the FEM simulation, to issue the perfect deformation sequence and the construction drawings of each tool. The successful feedback we are receiving from our customers is encouraging us to increase the capacity of this department with new hardware and resources.
Another theme dear to us is the service after market: technical assistance and spare parts, to keep the machines always in the best condition. Our products are designed and built to be durable, and our customers are expecting a long productive life. The availability of spares, even for machines born 40 years ago and more, is crucial. We are prepared with a large inventory in our warehouse of parts, ready to be delivered, minimizing the machine downtimes. All our branches and agencies, beyond the commercial activity, can give technical assistance. In the Limbiate HQ, we are boosting up the service with young resources and new structures.
To fulfil the requirements of Industry 4.0, Sacma is offering different packages to implement the machine data, at increasing levels, inside the network of the customer. Moreover, we started to investigate in the AI fields how to obtain additional information from those figures and how to make quick and useful for operators the instructions for setup and ordinary maintenance. As soon as ready, we will open to the market.
Last new, Sacma presents end of February, at the IWA Show in Nuerberg, the presses and rollers of the S-AMTEC line, special machines dedicated to the production of metal components for light munitioning. 85 years from his foundation, Sacma Group strives, day by day, to improve with innovation own products, not only the Sacma presses and the Ingramatic rollers, but also the feeding and unloading equipment of Tecno Lift and the tapping and turning machines of HS Aspe. We are always looking forward how to offer to our customers of the fasteners and cold forming industry a wider range of machines and services, making them more successful in the global competition. Of course, we do that because it’s our business, but especially because of the passion pushing us: we love to build top class machines and we like to see the satisfaction of our customers.
SACMA Group
warmer former SP470-WF
KSP12 Machine
Italy
manufacturer
fastener
bolt
cold forming
warm forming
扣件
國際展會
惠達雜誌
匯達實業
外銷媒合
廣告刊登
螺絲五金
五金工具
紧固件
台灣扣件展
印度新德里螺絲展
越南河內螺絲展
墨西哥瓜達拉哈拉螺絲展
美國拉斯維加斯螺絲暨機械設備展
波蘭克拉科夫螺絲展
義大利米蘭螺絲展
德國司徒加特螺絲展
wire Dusseldorf
FASTENER FAIR INDIA
FASTENER FAIR VIETNAM
FASTENER FAIR MEXICO
FASTENER POLAND
FASTENER FAIR ITALY
FASTENER FAIR GLOBAL
FASTENER WORLD
READ NEXT
Industry Activities
2024-05-24

Subscribe
