Industry Activities
Inside SACMA- The Smartly Integrated Plant Driving the Industry to Move Forward
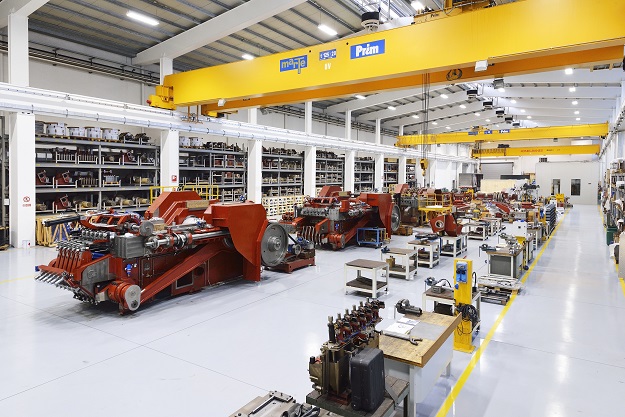

Add to my favorite
2020-01-16
When anyone is invited into the headquarters of Sacma located in Milan and passes through the long and full of sunshine aisle that leads directly to the areas where its customer-centric technology and paper-on products are made into reality, he definitely will not ignore the automotive engines for Audi, BMW, and Ferrari as well as the large propeller used for an aircraft, which are all assembled by those sophisticated parts manufactured with Sacma machines. These parts not only reveal the fact that Sacma is a reliable brand recognized in the global fastener manufacturing, but also represent the value it continues to create for customers that helps them win the trust of global leading manufacturers.
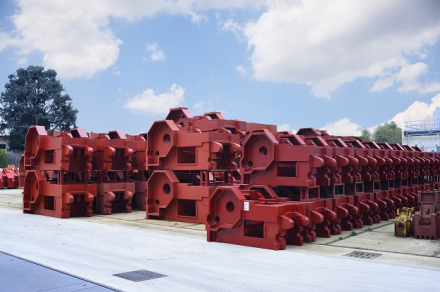
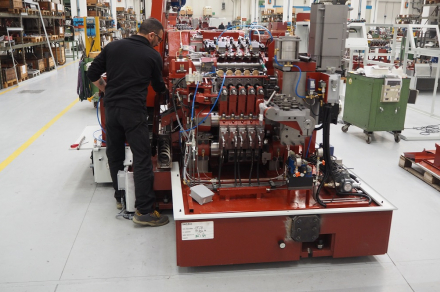
Vertically Integrated Manufacturing from Material Selection to Final Shipment
Use of High-Quality Materials and Advanced Systems from World’s Leading Brands
Use of High-Quality Materials and Advanced Systems from World’s Leading Brands
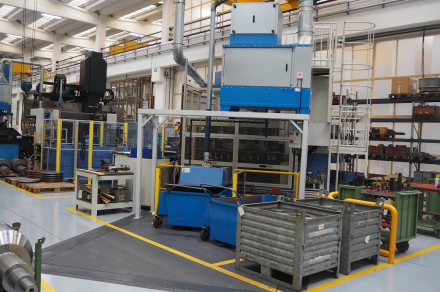
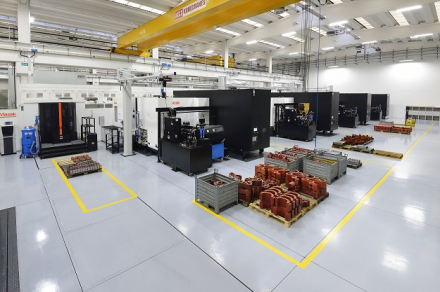
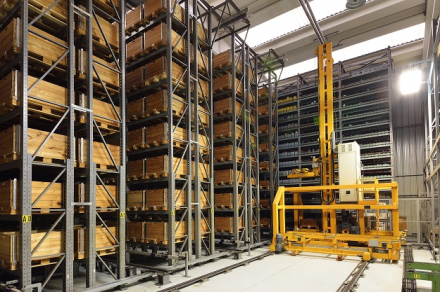
Being one of the few fastener equipment manufacturers in the industry capable of processing every step for machine manufacturing under one roof, Sacma specifically divided its Italy-based plant into separate zones for product R&D, preliminary simulation, software design, machine assembly, and functions testing, etc. Also, with the seamless collaboration with Ingramatic, OBM and Techno Lift, which altogether form the Sacma Group, it is able to assemble at least 70/80 sets of equipment per year, including Ingramatic thread rollers.
“Every detail matters” is imbedded into the mind of every SACMA’s employee. As a result, Sacma particularly uses high-performance ductile cast-die iron mainframes for its machines, which are then processed by PAMA machining centers, individual steel components are either grinded with Swiss-made Tripet high-precision CNC equipment or machined on MAZAK automated flexible manufacturing or turning systems, in order to achieve the highest quality and best overall performance. The gears are heat treated before machining, in order to enhance its durability and avoid unnecessary time for part replacement. Inside the plant, one can also feel the working efficiency by observing senior, well experienced technicians carefully assembling every part from mechanic to electronic to their designated position with a space-optimization logic.
“What Sacma is doing is helping you integrate every separate process into a more integrated one and save the costs for you,” says Valeriano Rampezzotti, President of the Sacma Group.
The Eco-friendly Oil and Liquid Waste Filtering and Recycling System
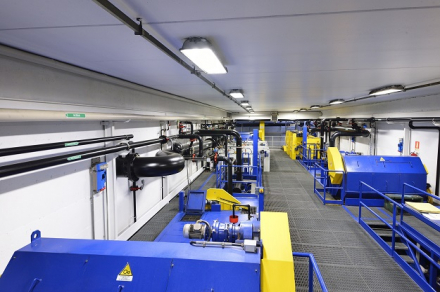
Besides making the best endeavor to create value for customers, Sacma also cares about the environment. It has established an in-plant system, which can filter and recycle used oil and liquid waste, fully compliant with local EPA’s regulations. According to Sacma, the used oil and liquid waste will be processed at this stage until they are proven to be not pollutant, and after that, they will be delivered back into the production line for reuse, which greatly shows the social responsibility and commitment of Sacma to establish a sustainable and environmentally friendly plant.
Experts That Completely Understand What Customers Need
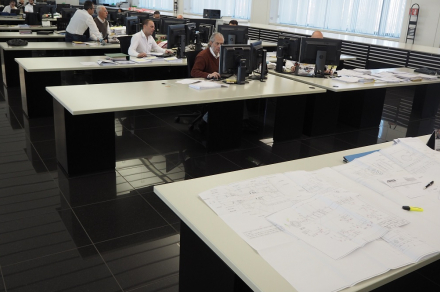
At Sacma, there is also a team of technicians and engineers, who not only have a wide knowledge of fastener manufacturing, but also have the capabilities to design and develop new machine models to satisfy the ever-increasing demand for special parts manufacturing. Through Sacma’s branches in Europe, America and Asia, the needs of customers in different countries can be quickly reported back to the headquarters in Italy, where the in-plant engineers with years of experience are ready to design solutions that best fit their needs.
“Our industry-leading technology can help manufacturers produce parts built with higher precision and strict tolerance, our professional team is also continuously dedicated to strengthen the design of our machine models with higher efficiency and better performance. With Sacma, “you can make everything that can be cold formed,” says Mr. Rampezzotti with confidence.
Sacma plans to exhibit at Wire Düsseldorf scheduled to take place from 30 March to 3 April, 2020 and present to the industry its latest models, including the new “S-Tooling Office” dedicated to tooling design, a new model KSP12R, which is a new generation 1D2B machine with thread rolling unit integrated, and a program of new secondary machines coming from a new company acquisition, all which will definitely make a hit in the industry again.
SACMA
SMART FACTORY
FASTENER MACHINERY
BOLT FORMING
扣件
國際展會
惠達雜誌
匯達實業
外銷媒合
廣告刊登
螺絲五金
五金工具
紧固件
台灣扣件展
印度新德里螺絲展
越南河內螺絲展
墨西哥瓜達拉哈拉螺絲展
美國拉斯維加斯螺絲暨機械設備展
波蘭克拉科夫螺絲展
義大利米蘭螺絲展
德國司徒加特螺絲展
wire Dusseldorf
FASTENER FAIR INDIA
FASTENER FAIR VIETNAM
FASTENER FAIR MEXICO
FASTENER POLAND
FASTENER FAIR ITALY
FASTENER FAIR GLOBAL
FASTENER WORLD
READ NEXT
Industry Activities
2020-03-30

Subscribe
