Osaka University Develops a Precise Pickup System for Screws and Parts
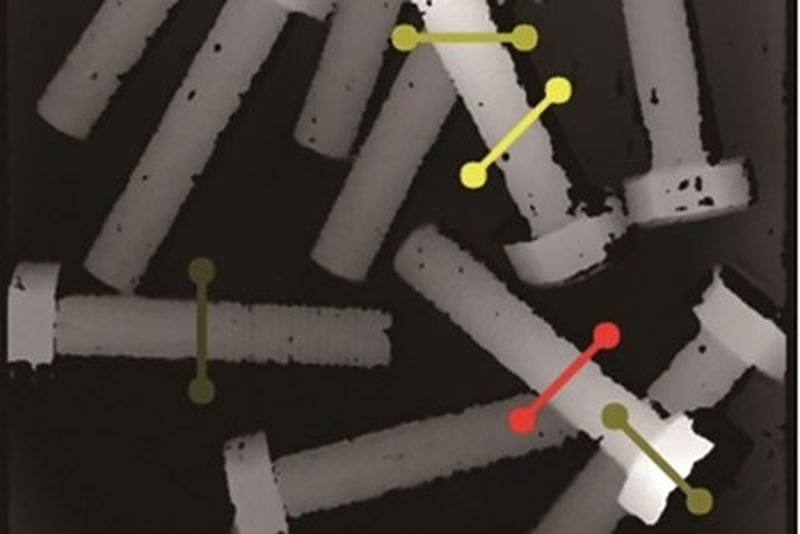

Professor Harada Kensuke from Osaka University developed a system for robots to accurately determine pickup locations in each operation. When the robot picks up a part, the camera measures the actual pickup location and its margin of error to the target location. The margin of error will be reflected on the next determination of pickup location. After a few times of confirmation, the margin of error will be rectified.
The rectification can be done just by simple mathematic determinants, and therefore, creates less burden. When picking up and placing a certain part, the robot only has to show the part to camera once for measurement and then it is done. In the professor's lab, he set an initial 10mm margin of error to the pickup operation of screws, and the margin was reduced to less than 5mm after several times of confirmation. This system is simple without requiring additional equipment, and therefore, its implementation is easy.

Subscribe
