Z & D Plating Co., Ltd. Launch of New Laboratory & Perfect Quality Check on Electroplating
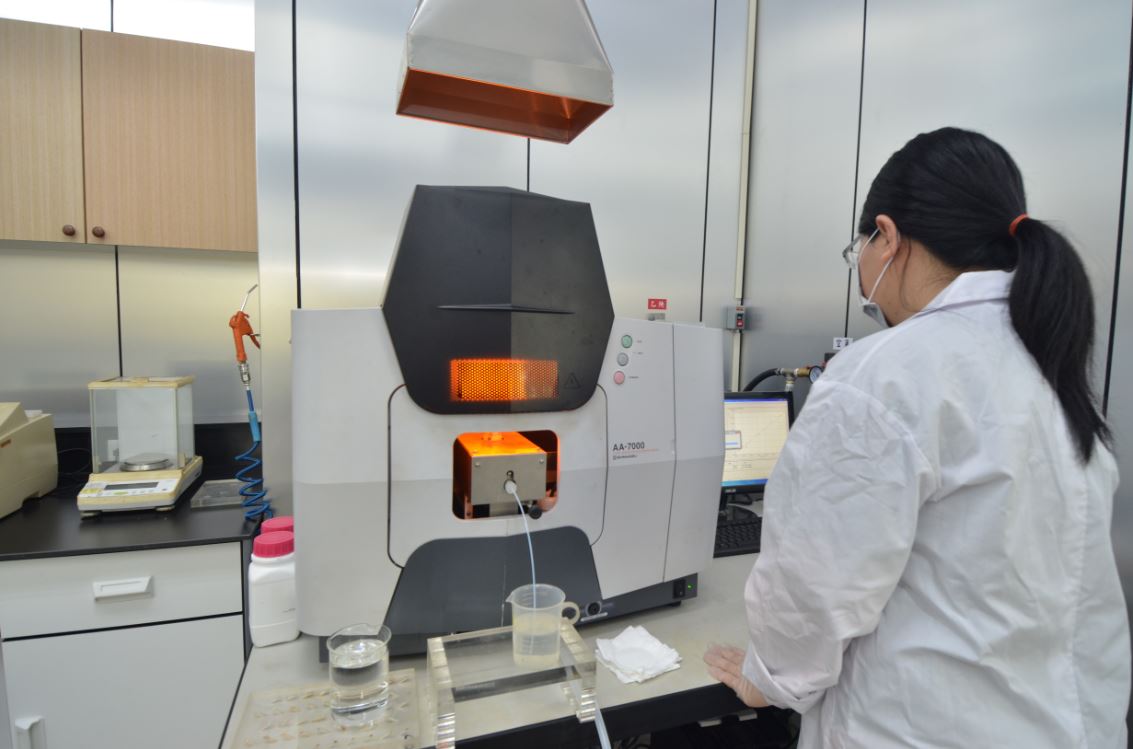
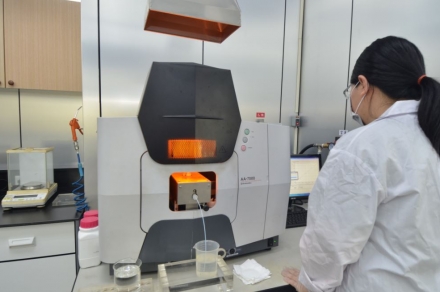
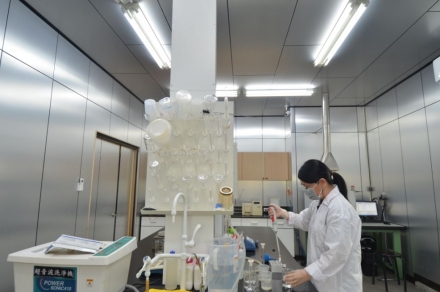
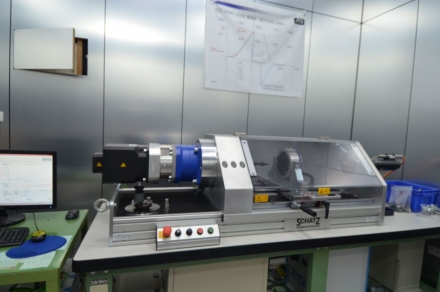
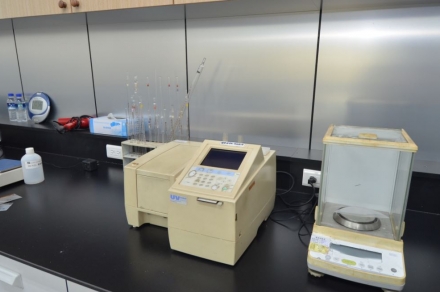

by Finnick Wu, Fastener World
Metal surface treatment, known as electroplating, is one of the necessary processing procedures for fasteners. Electroplating allows fasteners to be corrosion resistant and maintain good appearance, thereby providing more assembly options for subsequent products. Since the company was founded in Kaohsiung City of Taiwan in 2002, it has been dedicated to the study on metal surface. Currently it is the expert of high quality barrel galvanizing and galvanized zinc-nickel plating.
The company acquired IATF 16949 (2017), TAF lab (ISO/IEC 17025 (2018), ISO 14000 (2018) , and ISO 9001 (2017) certificates. It keeps improving technology to keep ahead of others in the industry. Now the newly completed laboratory is well-equipped and has increased experiment range to strictly monitor clients’ quality.
Professional Analytical Equipment
Achieving 200 hours White Rust & 1,000 Hours Red Rust Resistance
Fasteners require advanced lab equipment to strictly monitor electroplating quality. Therefore, Z&D’s lab has dedicated inspection equipment to check every process. The equipment include UV spectrophotometer (for liquid concentration), atomic absorption spectrometer (for zinc nickel, chromium detection), flame spectrophotometer, salt spray tester (for fastener anti-corrosion), X-ray (for coating thickness measurement), SCHATZ coefficient of friction tester. Z&D is the first electroplating company in Taiwan to adopt SCHATZ 2000Nm double head coefficient of friction tester with a speed of 75 rotations per minute. The tester is compliant to VDA235-203, ISO16047, and ISO2320 requirements.
ZinKlad-certified Quality
Monthly Capacity at 1,300 Tons
Besides lab inspection equipment, benchmark 3rd- party certificate is another critical criterium for clients to select collaborators. Z&D’s electroplating is certified to MacDermid ZinKlad (U.S.), so the production line can comply to a much wider spectrum of automaker regulations including BMW GS 90010, VW TL217, 244 FORD S437 S450, and JDM F15. Z&D is recognized by global major companies for its manufacturing technology and top quality. It has a host of long collaborating major companies including Fang Sheng Screw, Boltun Corporation, and San Shing Fastech. It has a monthly capacity of 1,300 tons and uses high quality electroplating liquids from major companies. Fast service, hospitality, capability in solving clients’ problems make up of Z&D’s primary competitive edge.
Full Dedication to Environment Protection for the Better Future
Electroplating industry is a highly pollutive industry. Z&D has worked hard on this issue and came up with a waste water discharge plant established within the company to fully comply with the requirements by City Environmental Protection Bureau. Electroplating liquids would go through related inspections two times per day before discharges. Despite reaching the government’s bar set for waste water, the company hopes to go further and do better and therefore expects to expand the water discharge equipment by the end of next year.
The current clients of the company cover not just the automotive industry but also other industries. Looking ahead, the company expects to increase the proportion of automotive parts. Additionally, it has a goal to apply for audit, continue to acquire certificates and keep up to date with the latest version to assure clients of premium electroplating quality.
Z&D’s contact: Ms. Yvonne Chiu
Email: ruida.xin@msa.hinet.net

Subscribe
