Alumseal® 611: New Zincate for Aluminum Alloys Designed to Extend the Electroless Nickel Process Bath Life
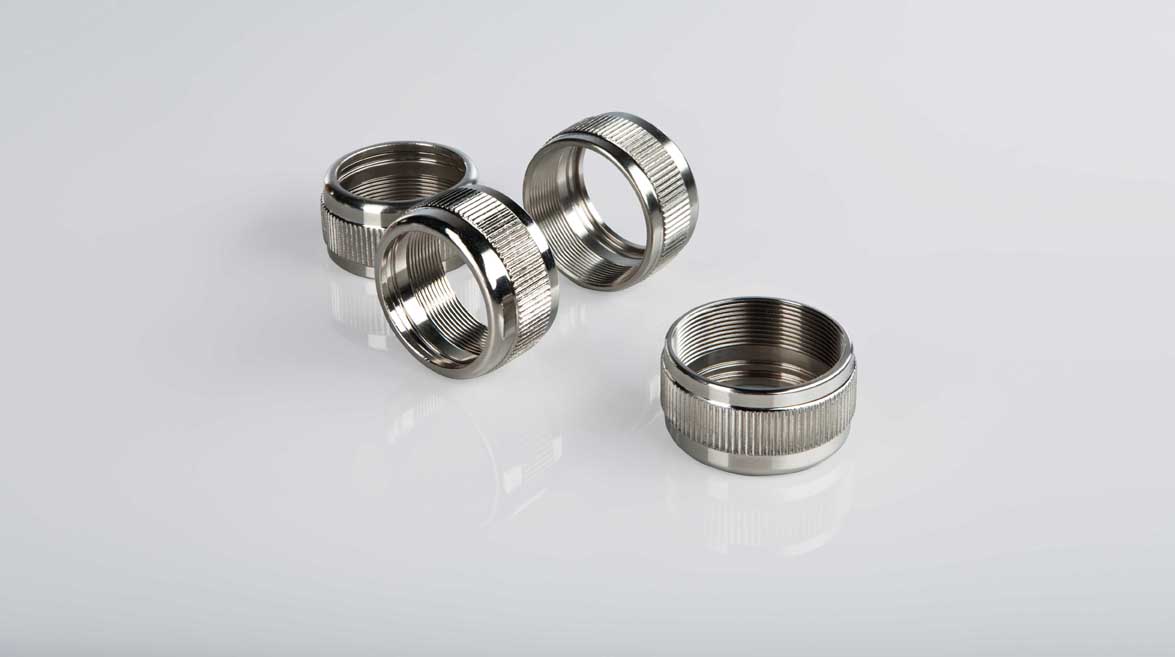

Aluminum is a very reactive metal and has a tendency to form an oxide layer very rapidly when in contact with oxygen. The presence of the oxide layer is not desirable in cases where the surface has to be metallized. The adhesion of subsequent coatings applied on the aluminum surface is adversely affected by the oxide layer. To avoid the rapid oxidation of aluminum during the pretreatment steps and prior to electroless nickel or electroplating, it is a common practice to cover the surface with a thin uniform film of zinc by use of a zincate process. In the case of electroless nickel (EN) plating, the build-up of zinc contamination limits the bath life to 3 – 4 MTO.
A new zincate process, Alumseal® 611, has been developed by Atotech to provide very thin zinc coatings in order to reduce the amount of Zn contamination in the EN bath, thus eliminating the need for an EN strike bath. Alumseal® 611 is designed to extend the bath life of the EN process to >6 MTO. Alumseal® 611 has demonstrated that coating weight of the zinc film is reduced by 30 – 60% on aluminum alloys when compared to existing zincate processes.
“When using the new Alumseal® 611 zincate process in combination with the high Zn tolerant electroless nickel process Nichem® MP 1188, the bath life can be extended up to 8 MTO without an EN strike bath”, states Shakeel Akhtar, Global Product Manager for Wear resistant coatings (EN) at Atotech. “Atotech is the first company to achieve this milestone within the plating industry.”
Due to low Zn build-up and high tolerance to Zn contamination, the efficiency of the EN bath is improved through higher average plating speed. The combination of Alumseal® 611 & Nichem® MP 1188 provides technical and economic benefits for the customer in a highly demanding industry.

Subscribe
