iTAC Laboratory--- TAF Certified Testing for Hardware & Fastener Industries
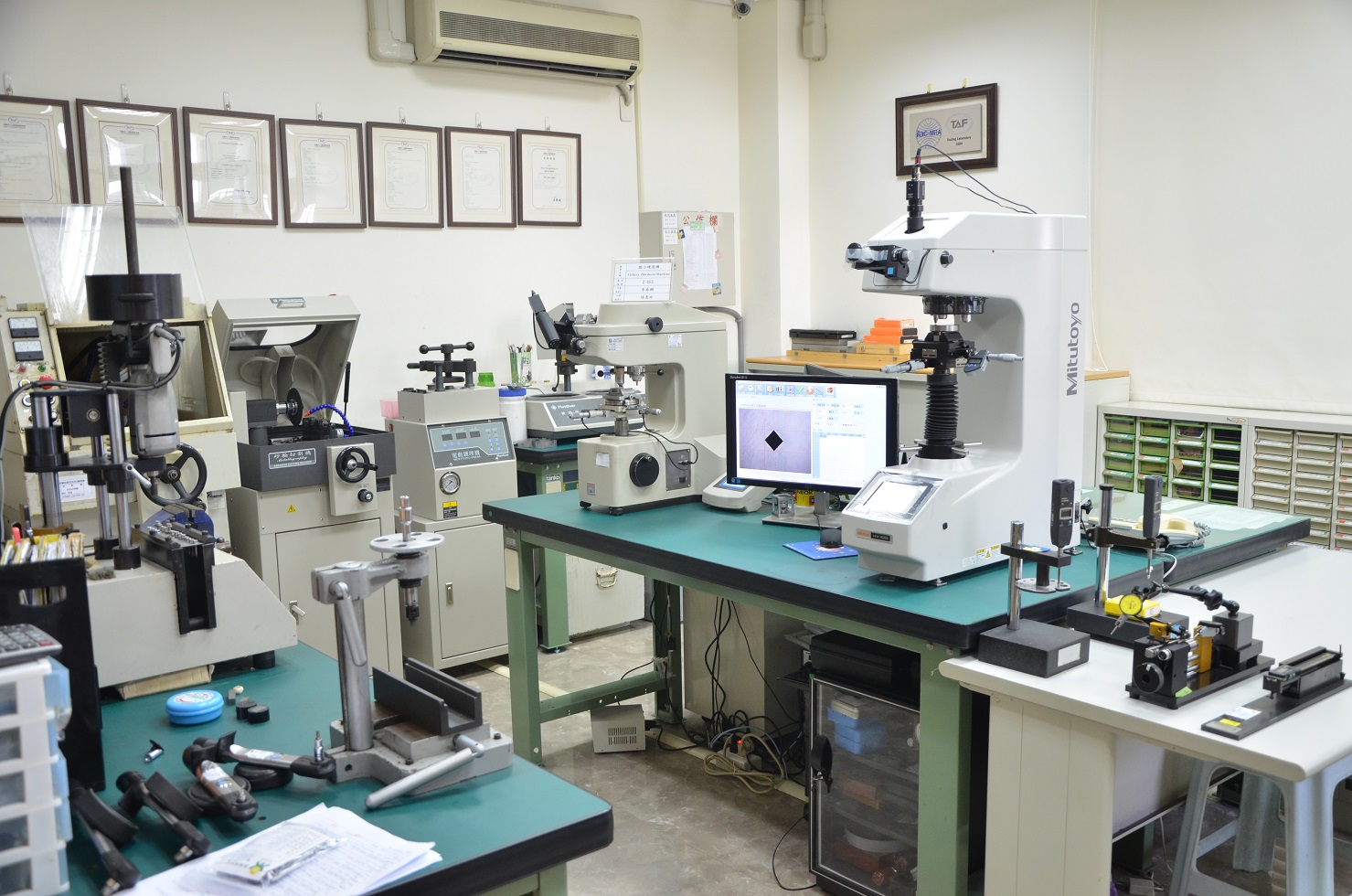
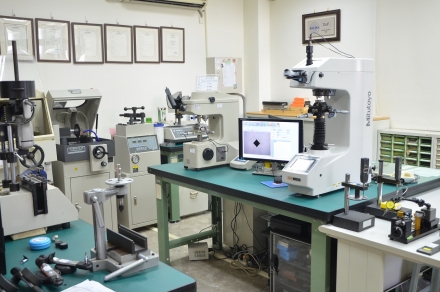
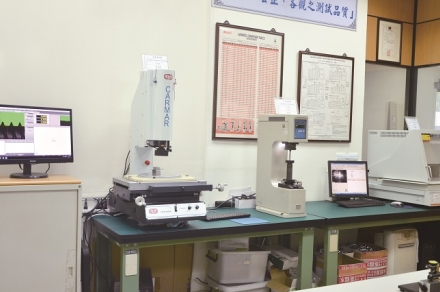
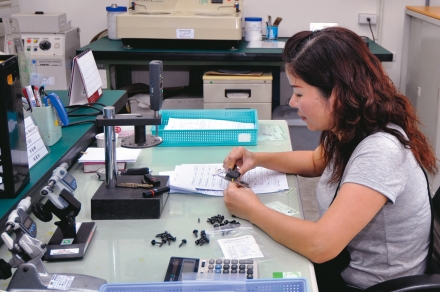

by Gang Hao Chang, Vice Editor-in-Chief of Fastener World
iTAC Laboratory Co., Ltd. founded in 2005 is a third party independent testing laboratory for fastener hardware and metal components. Within iTAC’s first year it successfully became a testing laboratory accredited by TAF ISO/IEC 17025, which is equivalent to United States A2LA accreditation. In addition to the third party lab inspection reports, iTAC can also offer many other quality inspection related services: (1) third party testing and inspection, (2) inspection services designated by customer location, (3) factory audits, CQI-9 audits, CQI-11 audits, (4) PPAP documentation & consulting, (5) laboratory outsourcing & subcontracting, (6) customized testing solutions, (7) other quality related documentation and consulting.
Managing director Charles Chang said, “TAF is one of the signatories of Mutual Recognition Arrangement (MRA) proposed by International Laboratory Accreditation Cooperation (ILAC) and International Accreditation Forum (IAF). Every inspection report issued by iTAC Laboratory is recognized and accepted by all member countries within the MRA.”
Targeting Problems for Customers Prior to Shipment
In iTAC’s experience with customers, product often shipped without any thorough inspection process taking place. We also found the testing standards cited by factories or by customers were not always in conformance with customers’ drawings and/or requirements. In addition, customers would use incorrect tools during inspection that didn’t identify the hidden potential failures of an item.
However, through the assistance of iTAC’s highly qualified team, questionable products sent by customers for inspection to iTAC Lab could be targeted prior to shipment. After inspection, customers are advised to make necessary changes or correct rejected material before any product is released avoiding costly returns and loss of time during transit.
Previously, when product wasn’t inspected prior to shipping the customer would reject the material after arrival. Not only would the customer lose valuable time during transit, but they potentially exposed rejected material to their customers due to lack of thorough inspection and testing methods. Managing director Chang added, “With our specialized and internationally recognized services, customers can significantly reduce the cost and enhance efficiency of dealing with supplier disputes.”
Moreover, iTAC also offers sample pickup, onsite inspection and many other customer-oriented services in order to respond to different customer requirements for product inspection. In addition to services in Taiwan, iTAC also has qualified inspection representatives by Yangtze Delta Region including Shanghai, Suzhou, Hangzhou, Jiashan, Haiyan and Ningbo, who offer onsite inspection services that help customers ensure the product quality for their orders in China.
Chang also noted, “We are very familiar with the standards and testing methods for the fastener and hardware industry. In addition, iTAC is continuously purchasing advanced equipment to satisfy customer demands. We also personally care about our customers. Through iTAC’s unique services and communication we try to satisfy our customers’ demands to strengthen customer relationships.
In the future, iTAC will keep “innovation, technology, accuracy and trust” as the four pillars of our business model and continue to provide customers with the most efficient and reliable service possible.
iTAC Laboratory contact: Managing director Charles Chang
Email: cchang@itac-lab.com.tw

Subscribe
