PINGOOD is Dedicated to Developing High Performance Plastic Fasteners
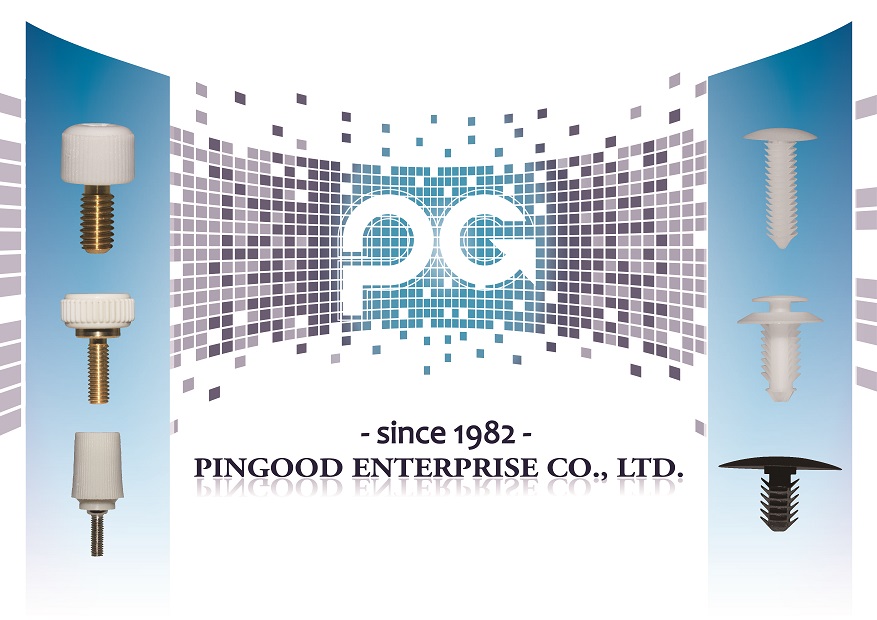

PINGOOD Enterprise Co., Ltd was launched in 1982 by the general director, Lin Mau Shen. Standing by the motto “Sustainable Management, Trustworthiness and Innovations.”, PINGOOD seeks new ideas and has been actively expanding its market with relentless determination to become outstanding in the future. Currently in Asia it has three plants located in ChongLi city in Taiwan, Dongguan and Suzhou province in China. The Dongguan plant is the largest covering an area of 36,000 m2 while the other two plants cover 12,000 m2 respectively. PINGOOD in Dongguan has an additional molding factory equipped with various Japanese machines and hires skilled engineers. Plus, it offers one-stop service. With acquired multiple skills, PINGOOD accomplishes products from design to manufacture without other assistance and further increases its competitiveness with a shortened time of molding development. It imports materials directly from international OEMs and also keeps track of the product quality from start to finish with the goal of ensuring the best buying experience for customers. Entrusted with international certificates, PINGOOD acquired ISO9001 and ISO14001 in 2003 and 2005 respectively, and as one of the global citizens its Dongguan plant attained the carbon footprint certification, and additionally its products and materials both meet EU standards of REACH and RoHS.
Widely Applied Plastic Fasteners
Plastic fasteners are the major products of PINGOOD. Fasteners on the market are mainly made of metal or metal stamping, yet for some special equipment and application such as chemical related fields, plastic fasteners are more effective and better to use because of their “Non-Corrosive” feature. Plastic fasteners are also a must for some equipment which suffers from the effects of electrical induction or electromagnetic wave attenuation caused by metal fasteners. Moreover, in the future IOT generation, the appliance of Wifi and other RF(Radio Frequency) will be more widely used, therefore the plastic fasteners undoubtedly will replace metal fasteners to some degree. Although plastic is not as firm or as solid as metal, through the development it’s been strengthened to meet the needs of different products.
Internationally Competitive Door Push Latches and Dampers
Plastic fasteners, the main product of PINGOOD, are mostly the components of industrial structures like door push latches, dampers, cable clips, PCB supports, LED holder, plastic screw rivets, and wires fasteners, etc. Apart from basic fasteners, PINGOOD has great confidence in its door push latches and dampers. The quality is surely comparable with the West and Japan. Both can be used in any board, and with a light press the board will be sprung open, opening and closing with ease with dampers, enhancing the products’ quality.
Effective Production and Precise Inventory Calculation
Facing the current challenge of customers’ demand for fasteners of less amount but wide variety, and the shorter life-span of materials, in order to keep up with the trend or even to surpass, more effective production and precise inventory calculation are two keys. Starting back in 2014, PINGOOD has been gradually updated with new machines. More than half of all are new Japanese TOYO molding machines and plus Seibu machines (WEDM and Sodick’s EDM). PINGOOD controls the quality strictly starting from mold designing and manufactures higher precision products with complete high-end equipment. Additionally, eco-friendliness is fully acknowledged. PINGOOD’s newly imported machines are all electric, therefore they decrease the electricity loss and improve production simultaneously. Furthermore, “More Automation and Less Human Resource”, the Dongguan plant applied the solar energy, the carbon footprint that’s saved is nearly equal to a carbon absorption of 800 trees. PINGOOD has 35 years of rich experience, hoping to replace flawed metal fasteners with plastic ones.
2018 New Product Release
Injection molding screws and automotive fasteners are both key series PINGOOD’s been developing. Installed with vertical and horizontal injection machines, the company can produce injection molding screws of its own, which is a corporate strength. Injection molding combines metal and plastic and other materials. The technique can reduce the assembling and labor cost, material size and weight, improving its reliability, strength and structure, and even enhancing the design flexibility.
Contact: Miss Jill Chen
Email: jill@pingood.com.tw

Subscribe
