Top Tips OEMs Should Consider When Purchasing Automotive Fasteners
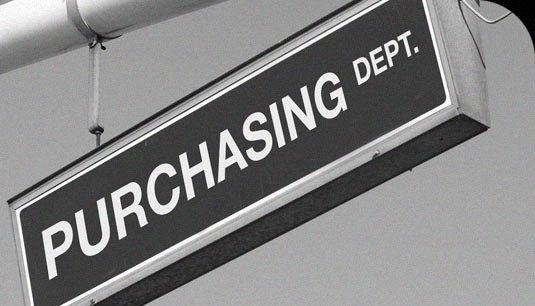

(Excerpt from Buckeye Fasteners Company's blog)
Automotive OEMs can eliminate or overcome production issues caused by fastening problems by using the design expertise of fastener manufacturers. It is essential to choose a manufacturer who not only has the expertise and capacity to meet strict specifications, but also can incorporate design features that save on assembly time and cost, while improving the quality and resilience of completed assemblies.
Below are tips to help OEMs collaborate with their fastener manufacturers to optimize the design and production process associated with the installation of their fasteners.
Include Fastener Engineers Early in the Design Phase
Early communication with a hands-on fastener engineer is essential in the automotive assembly process. The sooner the fastener engineer comes into the design phase, the better. Early input from the fastener manufacturer’s engineering staff helps you create a simpler design, saving OEMs significant costs and production time. Providing samples and prototype testing can aid in the selection of the proper fastener. One of the most common causes of budget overruns is over-engineering. Including your fastener engineer from the beginning in your design process helps improve assembly efficiencies, reducing or even eliminating problems down the line.
Choosing the Right Custom Fastener Manufacturer
Many times, a product design will push the OEM to require a custom fastener. However, custom fasteners are typically more expensive and time-intensive to produce. Choosing an experienced fastener manufacturer, who specializes in custom manufacturing is key to keep products on time and on budget.
The Simpler, the Better
Whenever possible, keep the design for the fastener as simple as possible. Your fastener manufacturer should be equipped with the knowledge to problem solve and create a simpler solution, which eliminates the need for multiple parts.
In 1928, Buckeye Fasteners first large commercial use of weld screws, were on the Model A Ford. The first HW weld screw was used on the frame of the Model A to allow one hand assembly of the fenders. The weld screw helped Henry Ford and the Ford Motor company revolutionize the assembly line process for manufacturing. More recently, Buckeye Fasteners worked with a major automotive manufacture to help develop a high strength weld fastener to secure the front bumper to vehicles.
Aim for Shorter Lead Time
With lead time being one of the biggest issues facing manufacturers today. Buckeye Fasteners’ broad range of stock fasteners provide off the shelf delivery on many items. It spoke about the importance of reshoring your fasteners and the many benefits that come with that. The more local your manufacturer is, the quicker your lead time will be.