Can’t Find a Good Electroplater? Modern Alloy Plating is Your Most Reliable Partner!
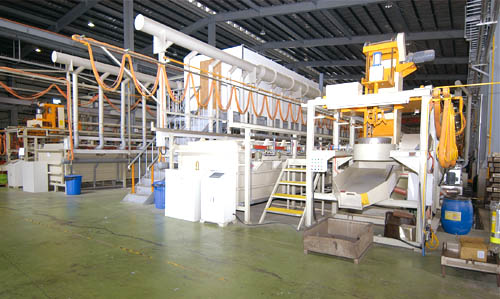
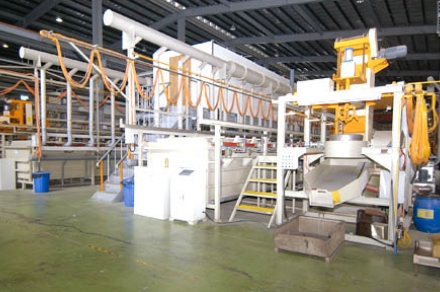
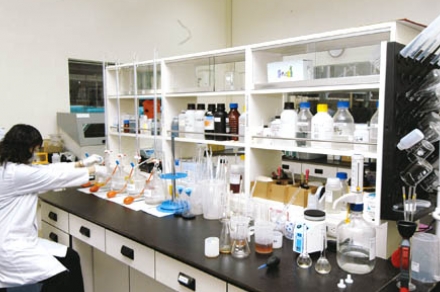
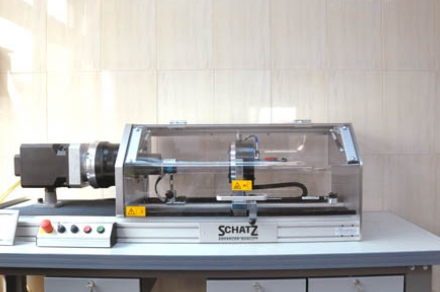
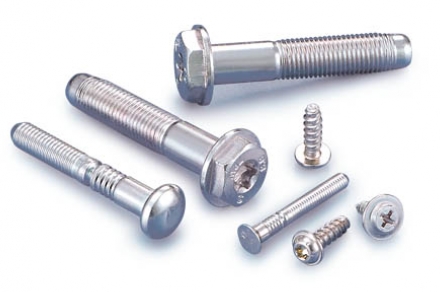

Modern Alloy Plating was established in 2005 providing surface treatment for various screws and nuts such as zinc-nickel alloy plating, acid zinc plating, alkaline non-cyanide plating, and mechanical galvanizing. Its alloy plating plant spanning 8,265 square meters in Benjhou Industrial Park in Ganshang District of Kaohsiung City has become operational since November 2006.
The alloy plating plant introduced Taiwan’s first passivation liquid recycling system from Europe. Unlike other traditional factories. Modern Alloy Plating controls quality through specialized technical talents, that is why it could become a rising star in the high-value surface treatment industry of Taiwan with its excellent equipment on par with German standards. The whole plant is arranged and designed to German standards. Notably, the passivation liquid recycling system is the first advanced equipment being introduced into Taiwan. The whole passivation line is fully automatic and more accurate on quality control, preventing human-made errors. Besides, each roller on the line is equipped with a rectifier underneath, which means more cost as compared to other electroplating plants that usually has a rectifier equipped for every two or three roller on the line. For high value products, heat treatment in addition to raw materials and technology is an important part.
With a great deal of investment in establishing the alloy plating plant, Modern Alloy Plating is very confident of it service. Its fully automatic electroplating line, fully automatic passivation line, passivation liquid recycling system, as well as lab precision instruments including AA Atomic Absorption Spectrometer, X-ray Film Thickness Analyzer, and Automatic Titration Analyzer are all controlled by professional talents through the whole process.
The company has been a Taiwanese alloy plating plant with the largest capacity and automated equipment.
* Its corrosion-resistant metal fasteners are treated with new technology that replaces harmful hexavalent chromium.
* Its nano-coating as a hole sealing technology can refill post-electroplating gaps after baking.
Interview with President THOMAS SHIH
Q: The automotive fastener market is on the highest priority of market development for Taiwanese fastener industry. Tell us about your technology and certification.
A: Heat treatment is a post-process for automotive fasteners and aims to extend the service life of products. Car manufacturers have stringent requirements on fasteners. The fasteners are required to be able to prevent corrosion and stabilize coefficient of friction (CoF). Towards these two aspects, our preparations include passing TS16949 certification and purchasing chemical liquids and CoF testers designated by car manufacturers. Meanwhile, we are applying for lab certification, improving our staff’s knowledge of car manufacturers’ requirements through training. So far, we have passed Renault and Daimler certification. Next, we’ll apply for BMW and GM certification.
Q: The business philosophy of your company is to make the best products of the world. Tell us more about this.
A: I fly to Germany as least 3 times a year to visit the biggest electroplating plant in Germany, and learn its electroplating technology as well as its most advanced equipment that is most capable of improving productivity, as I’d like to make Modern Alloy Plating localized and synchronized with German top quality. Through practical operating instructions, our fasteners’ corrosion resistance performance has surpassed our counterparts in Asia. Our belief is “Modern Alloy Plating, Make Astounding Protection”! In the coming year, we will also strive to improve equipment automation to enhance our production efficiency.
Q: A company lives on quality. how would you compare your electroplating quality, technology and price with European/American/Japanese companies? How do you control quality for your clients?
A: The manufacture of fasteners involves several different processes, so good quality control on every manufacturing process is the only way to making the final product meet car manufacturers’ requirements. Therefore, we always conduct pre-electroplating testing when fasteners arrive at our plant. If we detect any problem, we’ll immediately inform clients to come and check with us, and then we categorize fasteners of different dimensions and establish our exclusive manufacturing SOP, so that online engineers have operating standards to follow. We also have our men on the manufacturing line specifically for inspecting fasteners as well. If we detect any problem, we will return the fasteners to the previous manufacturing process. The final products will be tested for outer appearance and film thickness, and go for salt spray test. Such stringent quality control is to make the best products surpassing the ones from European/American/Japanese companies.
Q: When it comes to surface treatment, most people may start to worry about its pollution to the environment and its damage to human bodies. Do you have any recent eco-friendly policies or technology to cope with this issue?
A: Each time I fly to Germany, the focus of my trip is environmental protection and waste water processing equipment. The ongoing trend in Europe is to use advanced equipment to recycle and reuse waste water to turn electroplating into an eco-friendly industry and minimize the damage to the environment. In the future, we will continue with the introduction of state-of-the-art equipment into our plant to help address the waste water issue. Illegal waste water discharge is already the past. Now the one way to standing unwaveringly in the industry is to stick to the belief of eco-friendliness.
Q: With your experience in trade, fastener production/sales, and surface treatment, share with us your thoughts and feel about your 3-decade career life in the fastener industry.
A: Taiwanese fastener production has to seek higher added product value. Heat treatment is one of the most important added values for fasteners. It is usually heard in the industry that, if a standard fastener is applied with highly corrosion resistant plating, such as galvanization that can be free from white rust for 72 hours without hole sealing or zinc-nickel alloy plating that prevents white rust for over 120 hours, it becomes a special product with opportunities to draw clients and stay away from price cutting competition. Whether you are a maker or supplier, domestic or abroad, you are welcome to contact us if you want to place an order for high value added products, if you encounter surface treatment problems, or if you need related technology. We believe we can provide the best service with technology on par with the European standards.

Subscribe
