GM Adopts Smart Bolts to Solve Oil Leakage of Engines
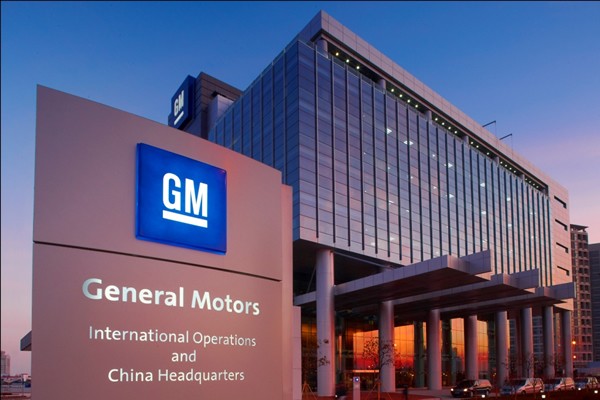

The engine manufacturing plant of GM based in New York State has adopted a new type of smart bolts, which can generate data during manufacturing to help car manufacturers reduce the possibility of errors. Many people know that the structure of engines is very complicated and may cause various problems during assembly, such as breakdown of assembly machines, defective parts, and of course manmade mistakes. However, the plant of GM based in Tonawanda, New York State has started to adopt some high-end techniques to prevent and find these problems. The key lies in the tiny bolts used in critical equipment.
It installed the “data bolts” onto the cylinder covers and main engine bodies. GM installed epoxy resin, storage chips (or RFID tags), and spiral wire (like an antenna) in heads of hollow bolts. All information shown on the data bolts will be uploaded to the server set up in the plant, which can help workers find and deal with breakdown of engines. Prior to the adoption of data bolts, workers might re-tighten the bolts during maintenance and checking, or even ignore the problems when bolts were not compliant to related standards, which would result in oil leakage soon or later. The single one computer-control machine tool costs about USD 1 million.

Subscribe
