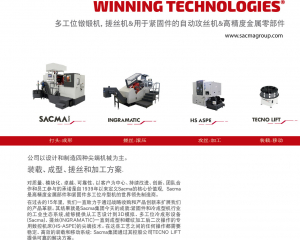
SACMA GROUP









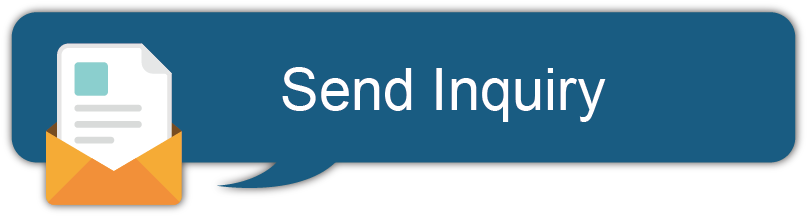
Commitment to Quality, Modularity, Excellence, Reliability, Customer Centricity, Continuous Improvement, Innovation, Team Working and Employees Engagement are the core values that have been defining Sacma since 1939, world leader manufacturer of multi-station cold forming machines for high-precision metal components and fasteners.
At our Headquarters in Limbiate, north of Milan, our 60.000m2 plant is the beating heart of Sacma Group. Here, through a insourced, fully vertically integrated and modular production system we are able to machine mechanical parts with the highest standards for precision and raw material quality that is second to none. Each workpiece is then assembled in-house and becomes part of either a Sacma multi-station cold forming machine or a Ingramatic flat-die thread roller, which then share the same destiny: accompany our customers for the next half-century in their workshop, rewarding them with the highest output possible 3 shifts per day.
In the last 15 years we have been dedicating our efforts in extending our product portfolio through strategic acquisitions and product innovation. The result is what Sacma Group is today: an industrial ecosystem for the fastener and cold forming industry, that is able to offer cutting-edge technologies from process design through 3D simulation, multi-station cold forming equipment (SACMA), flat-die thread rollers (INGRAMATIC) all the way to dedicated CNC machines for secondary operations after forming and threading (HS-ASPE). Anything that goes in between these steps requires stable, high-efficiency loading and moving systems: for this Sacma Group supplies reliable solutions through its controlled company TECNO LIFT.
1 Group, 5 interconnected Production Sites within 100Km range, 300 Employees worldwide, 5 Foreign Branches with local after sales staff (USA, China, Taiwan, Germany, Brazil), 24 Agencies, 81 years of history, 24/7 onsite an d remote service: Excellence for our customers.
ALL IN ONE: KSP12-R
Sacma World Premiere: New Double Blow Header model KSP12-R with threading unit.
Sacma Group is well known for the designing and manufacturing of Combined Headers which are able to produce fasteners from M4 to M24.
These Combined Headers can produce finished parts like fasteners and screws for the automotive industry, starting from the wire and are the best solution for high productivity requirements, consolidation of production methods, floor space utilization and work flow in the fasteners manufacturing process by having the forming, pointing and thread rolling all in one machine.
To complete its whole range, Sacma is introducing the new combined header model KSP12-R to run fasteners that range from M3 to M8 with a maximum shaft length of 60 mm. The machine is a double blow header with an integrated threading station, representing the new generation of the worldwide known KSP11-R. Sacma is re-introducing in the product line the 1D2B combined header to face an increasing request of small and self-tapping screws widely used in different industry fields.
The KSP12-R combines typical SACMA solutions, proven by thousands of machines, with the most advanced mechatronic technology available in the market. The one-piece main frame, perlitic cast iron, normalized, natural aged for at least 12 months, high precision machined, is a guarantee of rigidity and stability for all machine life. Major set-up adjustments are now motorized for a quick and friendly changeover: S-feed wire feeder driven by a torque motor, motorized wire stock gauge and DKO, threading starter driven by torque motor with self-learning function.
The quality management is facilitated by two gates interfaced with the load monitoring system and discharging of NC parts, after the header and after the roller. An optional sophisticated load control system protects the machine against overloads and monitors the forming and rolling processes. Scraps separators in different sizes are available when producing self-tapping screws.
All these features make the KSP12-R the best value for the Customer’s investment, especially when running parts traditionally by a line of connected machines. This ALL-IN-ONE high productivity process allows to quickly return the customers investment. These legendary long life SACMA machines guarantees future profits thanks to the following concept:
VS production floor / sqm: the relation between the floor utilized by a 1D2B combined header against a line of connected machines (1D2B header + conveyor + roller) is normally 1 to 3.
VS production floor / ppm: consequently, more parts produced per area make the overall plant more profitable and efficient.
VS manpower: one combined header requires one operator. More often one operator manages two or three small combined headers. In case of separate machines, only one operator is not enough to attend this many lines.
VS maintenance: more machines mean more maintenance. The Combined machine is only one machine that does two operations, therefore less maintenance is required.
VS changeover time: the total time to set up two different machines, with related feeding systems, is higher than the one of combined machine.
VS eco-friendly: having a Combined machine, with the header and threader enclosed in one soundproof enclosure, allows all of your coolant and oils to be recycled safely and controlled in one sealed area: no oil leakage, less pollution, clean and safe working place .
VS start up time: all Sacma machines are recognized as “quick plug in” equipment. The KSP12-R is ready just a few hours after the installation, and is quickly ready to start production. The advantage remains when necessary to update the factory layout. Only one machine needs to be fixed to the floor, and connected to the air plant and the power supply.
VS energy consumption: only one motor for two operations is more efficient than several motors. Combined headers consume less than two machines and the power monitoring becomes more simple and more convenient.
VS Tool life: the forged parts still warm and oiled are placed in the roller. Thanks to this, the flat dies last a lot longer, reducing the running costs and increasing the production efficiency.
The orders for this innovation have already started and the first machines will be delivered within 2021!
Heading Machine
Hollow Heading Machine
Multi-station Cold Forming Machine
Nut Formers
Nuts Tapping Machine







Heading Machine
Hollow Heading Machine
Multi-station Cold Forming Machine
Nut Formers
Nuts Tapping Machine
Parts Forming Machine
Rollers Formers
Screw (Bolt) Formers
Screw Washer Assembling Machine
Self-drilling Screw Forming Machine
Semi Tubular Rivet Machine
Set Screws Formers
Sockets Formers
Thread Rolling Machine
Warm Former
Automatic Conveying System
Blind Nut Formers
Blind Rivet Heading Machine
Cold Header
-----
Designer and manufacturer of progressive headers which are available in several models up to 33mm diameter cutoff capacity and feature the most advanced controls and systems for forming net and near net shapes with consistent and repeatable tolerances up to 350ppm max. In addition, the combined headers including the heading, the pointing and the threading units are supplied for the production of screws and bolts in one step. These machines determine maximum efficiency and quality in the manufacturing process of standard fasteners and special automotive fasteners, because they supply the finished product. The fully integrated Warm Formers complete the large range of Sacma machines for the Aerospace and Automotive markets to run special materials. For the forming of special components, the formers are all available with modular high-tech packages to extend the possibility of the cold and warm forming technology. Sacma also supplies a full service with technical centers around the world, 100% spare sparts and the S-Tooling division to support the customers for new challenges.
INGRAMATIC
----------
Designer and manufacturer of innovative thread rolling machines. From TR00/W000 to TR9/W70, the “I-Thread” machine line provides innovative features like the motorization of the die match adjustment, the single/double starter unit driven by torque motor/servomotor, the full-motorized adjustments from touch screen panel and the QTC washer assembly unit and pointing machines. Ingramatic provides combined rollers for complex parts with rotative and flat dies stations, all in one, to run multi-shape parts in one shot. The unique design of the one-piece bed frame including the reaction block makes the Ingramatic rollers the most advanced and durable machine worldwide. As per Sacma, additional packages may be add to the configuration of the machines to extend the possibility of the threaders as the headless parts feeder, the loading systems and the Warm Forming unit.
HS ASPE
-------
HS Automazioni srl supplies a wide range of automatic machines to run pre formed parts obtained by cold and warm forming. It is the logical step which was requested from the Sacma customers looking for a complete turkey solution from one solid and stable supplier making everything inside.
The company designs and manufactures a range of machines branded HS ASPE. Which is consist of tapping machines, combined machines, transfer machines and multi spindle turning machines. HS ASPE is following the industrial strategy of the Sacma Group with outstanding assembly lines divided by product family and following a modular system concept with serial production to make the machines extremely precise and durable.
TECNO LIFT
----------
Tecno Lift can offer the best solution to ease the production process, taking into account the type of fastening elements to be moved and the working speed. The Tecno Lift range is consisting of vertical elevators to be connected directly to the feeding rails of machine tools; vibrating hoppers to load the blanks and washers into the vibratory feeders ; Porter unit with combined weighing hoppers for the precise and accurate feeding for small and medium sizes parts; belt feeders to load the blanks into a vibratory feeders and other vibrating systems giving a constant and precise quantity of blanks; belt conveyors for parts or scraps; sub-batching units allowing to split a large production batch into manageable sub-batches so that they can be controlled easily during the process and; bin tilting elevators for a complete automation of the loading system with the possibility to lift and rotate the containers.


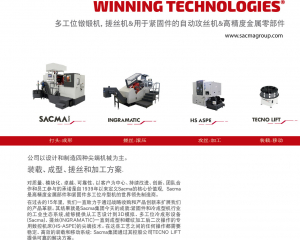
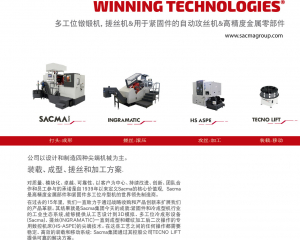
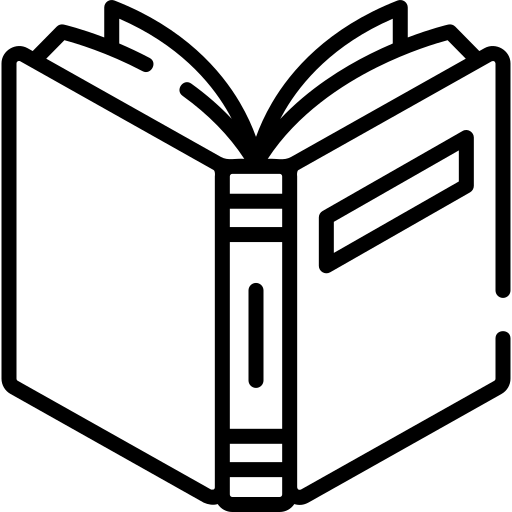
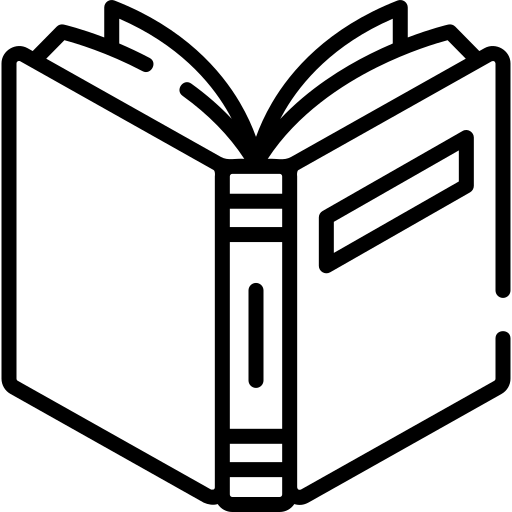
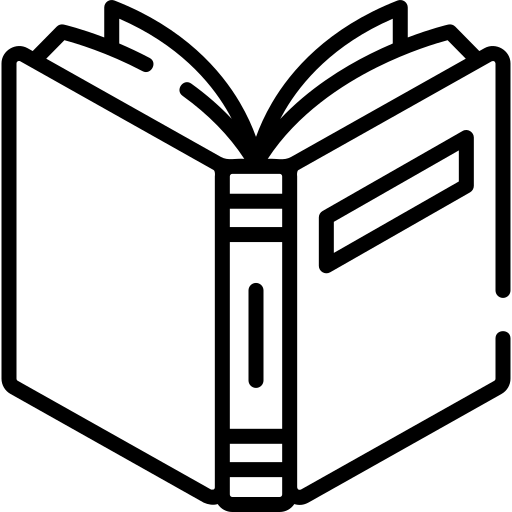
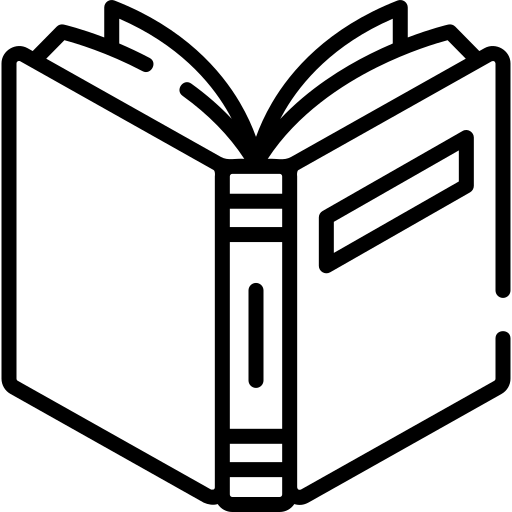